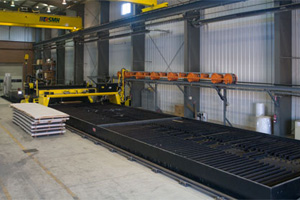
In industries where cost and time efficiency are of greatest importance, plasma cutters and cutting methods are widely used. For example, construction and engineering companies rely heavily upon plasma cutting. Materials that are the cornerstone of such industries are generally expensive and require fine precision cuts with minimal waste. Plasma cutting is capable of delivering precise cuts to a wide range of materials in a reasonable timeframe and at efficient cost.
Why Use Plasma Cutting?
Advancements in industrial cutting have seen the introduction and application of many different cutting techniques over the past several decades. However, many laborers, hobbyists and artists depend upon both the accessibility and precision of plasma cutting to render top results on their materials.
Cutting with plasma offers many benefits over other industrial cutting methods such as the following:
-
Is able to cut all metals that are electrically conductive such as stainless steel, copper, aluminum, and brass
-
Can gouge and pierce material
-
Reduced heat-affected zone. (This prevents materials from distorting or warping. In turn, less material is wasted.)
-
Cutting time is fast, up to 130 in. per minute
-
Cuts are precise
The above points have made plasma a top choice in industrial cutting methods. The high speed and high precision capabilities makes plasma an efficient means of cutting heavy-duty materials for a wide range of industries.
What is Plasma?
In short, plasma is a gas that is ionized and is able to conduct electricity when it is in its forth state of matter. It develops when an electrically neutral gas is combined with energy.
When energy is added to plasma, the arc becomes increasingly hot. As such, the gas is constricted and pushed through a nozzle with intense pressure. The pressure and the heat of the arc are controlled by increasing and decreasing the amperage. The hotter the arc, its abilities to cut through thicker materials increase.
When plasma cutting was first introduced, it was quickly noted for its ability to make efficient cuts in metal. It was preferred over traditional methods such as sawing, as it offered minimal mess, accuracy and ability to cut both extremely thick and electrically conductive materials.
In addition, cutting with saws left jagged edges on materials that were rather expensive. Plasma cutting reduced the amount of materials that went wasted as it delivered smoothed edge cuts.
However, the first plasma cutting machines were slow and the process was not very cost-efficient. Therefore, plasma cutting was mainly applied to mass cutting projects that required the same shapes to be made to many pieces of material.
With advancements in the industry, plasma cutting soon became one of the most commonly used metal cutting methods. Handheld plasma arc torches offer hobbyists and artists sufficient means of completing their own plasma cutting projects, without having to source out a body shop or welder.
While plasma cutting can be done in a domestic setting, such as a personal workshop or garage, it is highly recommended to have a professional handle plasma cutting requirements, due to specific safety measures that must taken.